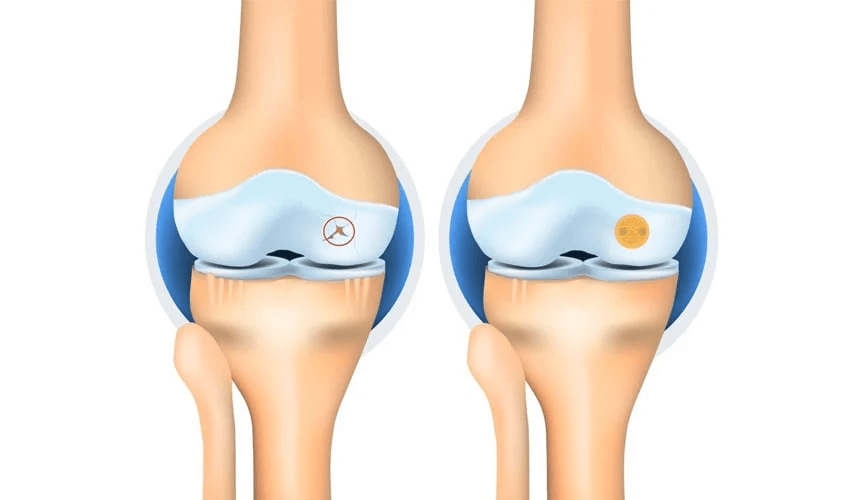
Founded in 2016, Nanochon aims to facilitate cartilage replacement and repair in patients suffering from knee injuries. The company relies on 3D printing technology, specifically extrusion, to produce an implant that replaces lost or damaged cartilage. Nanochon thus offers an alternative to arthroplasty, a method that is often painful for patients and involves a very long recovery. Called Chondrograft™, this 3D printed device is made from an innovative biocompatible composite material that promotes tissue growth. We caught up with one of Nanochon's co-founders and CTO, Nathan Castro, to learn more about this implant and the company's outlook.
Q: Can you introduce yourself and your relationship with 3D printing?
My name is Nathan Castro and I am the co-founder and CTO of Nanochon, Inc. We are developing a 3D-printed synthetic implant for cartilage repair in the patellofemoral (knee) joint. I discovered additive manufacturing and 3D printing in the mid-2000s during my undergraduate studies at the University of Texas-El Paso while participating in an undergraduate research program at the WM Keck Center for 3D Innovation. I focused on the synthesis of biocompatible resins for stereolithography. I continued my interest in stereolithography during my PhD, during which I built a benchtop system and expanded my research to musculoskeletal tissue regeneration.
Question: : How did Nanochon come about and what is its purpose?
Nanochon is a spin-off from George Washington University, where co-founder Ben Holmes and I completed our PhDs in regenerative medicine. We were introduced to entrepreneurship through the local NIH I-Corps (DC), where we conducted several customer discovery interviews to test our technology. At the end of the program we decided to join forces and Nanochon was created. Our goal is to address the unmet need for effective and efficient cartilage repair using a materials and mechanics based approach.
Q: How are Nanochon implants manufactured?
Nanochon's ChondrograftTM is further manufactured by fusing strands of our proprietary biocompatible composite material. The raw microstructure is created by the 3D printer. In addition to the visible microstructure, ChondrograftTM also features sub-micron porosity, which after post-processing results in a softer, more flexible device while maintaining its integrity. Our goal is to address the unmet need for effective and efficient cartilage repair by applying a material and mechanical approach. What sets Nanochon apart from the rest is our unique 3D printing material that produces a mechanically strong and biocompatible implant.
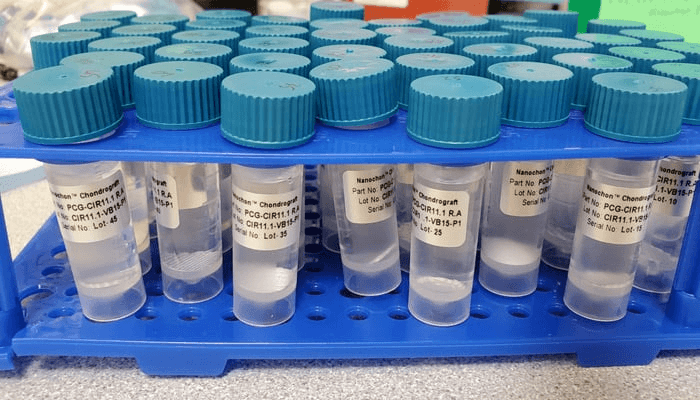
Q: What are the main advantages of additive manufacturing for Nanochon?
We believe that additive manufacturing offers multiple advantages, especially for small startups like Nanochon. Here are some of the specific benefits: 1) it allows rapid design iteration and testing; 2) offers cost-effective production on a small to medium scale; 3) enables capital investment management thanks to the variety of FFF printers available and the robustness of these systems, allowing good levels of reproducibility and repeatability.
Q: What should be considered when using 3D printing in the field of medicine?
In our experience, it's important to talk to knowledgeable people in this area. Regulatory guidance is particularly important because additive manufacturing is still a relatively new area of direct medical device manufacturing. Although guidance documents exist, they are only guidelines and are open to interpretation. Keeping in touch with people with direct experience will minimize unnecessary obstacles. Market size and product design are also important considerations. Nanochon positions ChondrograftTM as a ready-to-use implant suitable for a wide range of patient categories. The possibility of a customized or standard product should be considered and evaluated to determine the most appropriate course of action.
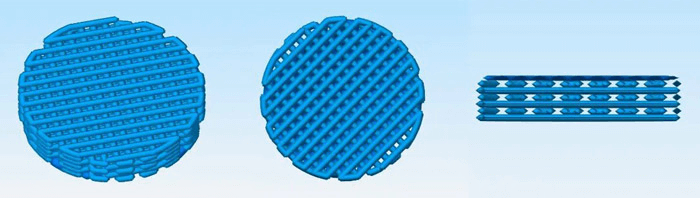
Q: How do you see the future of additive manufacturing in medicine?
I firmly believe that the future of additive manufacturing in medicine is bright, and that as the technology continues to develop, new materials become available, but there are still opportunities to explore.
Q: Any final words for our readers?
From a personal perspective, additive manufacturing awakened the inventor in me by providing me with a tool that allowed me to be creative and test my ideas. A small investment can pay big dividends. Not only financially, but also spiritually.
0 Comments